I. Working Principle:
The working principle of the ZGJ series drum flaker (dryer) involves a cooling crystallization process. Molten material in the feed pan contacts the cooled drum, forming a film on the drum's surface. Through heat exchange between the film and the drum, the film cools and crystallizes. The crystallized material is then scraped off by the blade, resulting in flake products. Drum drying is a continuous operation device where the rotating drum heats and dries liquid-phase materials or sheet-like materials attached to the drum's outer wall through heat conduction.
II. Application Range:
This device is suitable for various materials with melting points below 300°C.
III. Typical Materials:
Polymer Products: Low-density polyethylene oligomers, petroleum resins, oxidized polyethylene, etc.
Organic Chemical Products: Phthalic anhydride, maleic anhydride, naphthalene, polyglycols, higher fatty alcohols, chloroacetic acid, trimethylolpropane, guanidine nitrate, bisphenol A, isophthalic acid, etc.
Inorganic Chemical Products: Sulfur, sodium sulfide, caustic soda, sodium hydrosulfide, calcium chloride, etc.
IV. Technical Advantages:
· Performance is domestically leading.
· Compact structure, small footprint.
· High drum precision, good product uniformity.
· Multiple blade sets with flexible adjustment.
· Semi-pipe jacketed feed pan for safety and reliability.
· Equipped with side blades to prevent material buildup on the sides of the drum.
V. Structure Description of the Flaker:
The drum flaker consists of a drum, blade system, feed pan, frame, hood, and transmission system. The components are described as follows:
Drum:
The drum is the core of the equipment, comprising the drum surface, end plates, driving shaft, driven shaft, and support rings. The drum surface is made of SUS304 stainless steel, while the end plates, driving shaft, driven shaft, and support rings are made of carbon steel. Key technical control points include the surface quality of the drum, the concentricity between the drum surface and the driving/driven shafts, and the concentricity of the inner circle at the shaft ends.
The drum surface, drum shaft, and drum sides are processed in a single operation using a large CNC horizontal lathe. The outer cylindrical surface of the drum is polished using a grinding head, ensuring high straightness, roundness precision, and surface finish, which guarantees the quality of the flakes.
Blade System:
The blade system employs a multi-blade configuration popular internationally, consisting of main blades, side blades, blade rods, adjusting handwheels, blade holders, positioning shafts, guide plates, and related accessories. The main blades range from 4 to 16 sets, and the side blades consist of two sets. Each main blade is supported by bearings and can be adjusted using a handwheel. The system includes an elastic protection mechanism and self-locking device to prevent blade damage to the drum. Side blades at both ends of the drum effectively prevent material accumulation at the drum sides. The main blades are made of high-density resin boards, while the side blades are made of 304/316L stainless steel. The materials in contact with the product, such as guide plates, blade rods, blade holders, and positioning shafts, are made of SUS304/316L stainless steel. Carbon steel or cast steel is used for adjusting handwheels, support seats, and related accessories.
Cooling System:
The cooling system employs a spray cooling design consisting of a distribution pipe, central pipe with round holes, inlet pipe, outlet pipe, siphon pipe, and compressed air inlet. Compressed air is introduced through the central pipe to expel the cooling medium that accumulates at the drum bottom, maintaining a low water level inside the drum.
Main features: This system represents our third-generation cooling structure, enhancing the spray cooling mechanism. The working principle involves the cooling medium (usually low-temperature cooling water) being sprayed onto the inner surface of the drum through the spray system, covering the entire internal drum surface with overlapping layers of high-speed water flow. This quickly cools the surface, allowing rapid heat exchange between the drum wall and the molten material film attached to the drum's outer surface. As the drum rotates, the high-temperature liquid material rapidly cools into a solid, undergoing a three-step process from high-temperature liquid to a solidified state. The cooled medium collects at the lower part of the drum and continues exchanging heat with the material at the bottom before being expelled through the cooling medium discharge pipe.
Due to the high water flow speed during the spray cooling process, the heat transfer coefficient (K value) is large. The equipment structure is relatively simple, scientifically designed, and can adjust the temperature gradient to suit materials with different melting points by varying the arrangement and number of spray nozzles. This is an advanced and popular drum cooling method internationally.
Feed Pan:
The feed pan comprises a material pan, semi-pipe jacket, feed inlet, overflow outlet, and other process ports. Material enters the feed pan through the feed inlet at the bottom of the flaker and is taken away after contacting the drum. The overflow outlet on the feed pan controls the liquid level, facilitating the adjustment of the drum immersion depth. The feed pan has a semi-pipe hot water jacket to ensure the material inside remains molten. All material inlets and outlets are equipped with hot water jackets to prevent material solidification.
Transmission System:
The transmission system includes a motor, reducer, gears, and sprockets. The motor and reducer drive the drum through the engagement of a small gear with the large gear on the drum shaft.
Hood:
The hood is made of stainless steel and forms a sealed chamber with the feed pan to enclose the drum. The seal between the hood and the drum shaft ends is maintained using packing seals to prevent leakage of harmful substances. The top of the hood has an exhaust port connected to a fan duct. The hood is equipped with a hot water companion pipe to prevent the accumulation of sublimed materials. The junction of the hood and the blade has inspection ports and sight glasses for operational convenience. All materials used are SUS304/316L stainless steel.
VI. Specifications and Models:
Specification |
Drum Dimensions mm |
Motor Power kW |
Drum Speed rpm |
Approximate Dimensions (mm) |
||
|
|
|
|
L |
W |
H |
ZGJ-1 |
600×600 |
2.3~3 |
0.3~15 |
2400 |
1480 |
1410 |
ZGJ-3 |
800×1200 |
3~3.5 |
0.3~15 |
3360 |
2000 |
1600 |
ZGJ-4.5 |
1200×1200 |
5.5~7.5 |
0.3~15 |
3730 |
2250 |
2050 |
ZGJ-7.5 |
1400×1800 |
5.5~11 |
0.3~15 |
4460 |
2460 |
2350 |
ZGJ-9a |
1200×2400 |
7.5~15 |
0.3~15 |
5610 |
2250 |
2050 |
ZGJ-9b |
1600×1800 |
7.5~15 |
0.3~15 |
4460 |
2600 |
2550 |
ZGJ-18b |
1600x3000 |
18.5-22kw |
0.3~15 |
4680 |
2600 |
2550 |
ZGJ-20b |
1800x3000 |
18.5-22kw |
0.3~15 |
4785 |
2760 |
2720 |
ZGJ-22 |
2300×3000 |
22~30 |
0.3~15 |
7200 |
3900 |
4120 |
VII.Equipment Pictures:
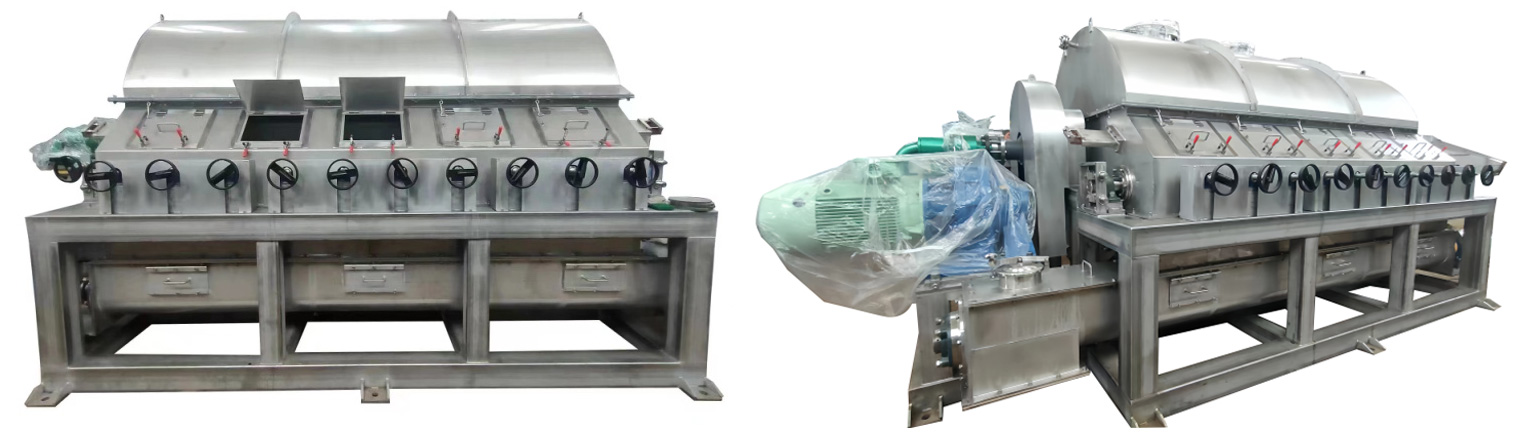